August 2024 | 1611 words | 6-minute read
The road stretches out ahead as far as the eye can see, amidst an endless expanse of water, as you glide along the 21.8km Atal Bihari Vajpayee Sewri–Nhava Sheva Atal Setu, also known as the Mumbai Trans Harbour Link (MTHL). Inaugurated in January 2024, the Atal Setu connects Mumbai with Navi Mumbai, and is the longest bridge and sea bridge in India, and the 12th longest sea bridge in the world.
As is the case with many landmark Indian projects, a Tata company has been instrumental in its construction. The bridge was divided into three packages for construction and Package 2, which consists of a 7.8km stretch, including over water and with an interchange, has been built by Tata Projects in a joint venture with the South Korean company Daewoo E&C. The JV won the bid for the phase in December 2017, at a contract value of ₹5,612 crore ($850 million). “We feel a sense of satisfaction and achievement that our company helped execute a significant part of a project of this stature,” says Vinayak Pai, Chief Executive Officer and Managing Director, Tata Projects. “We have set benchmarks in quality, safety and environmental standards, and showcased global synergy and collaboration among all stakeholders, including local communities, and, most importantly, the diverse wildlife that resides here.”
Anchoring marvels
Package 2 of the bridge commences a little after the 10km mark if one is travelling from the Mumbai city side at Sewri and includes the interchange on the Navi Mumbai side. The ambitious infrastructure project showcased Tata Projects’ innovative thinking and deep technical expertise in navigating engineering and logistical complexities involved in constructing bridges over water bodies. Construction began in March 2018, at Shivaji Nagar, Ulwe, Navi Mumbai, with the establishment of a casting yard and a crucial 2km-long temporary access bridge for the intertidal section, the area where the Arabian Sea meets land.
“This landmark project involved complex marine and foundation engineering, as it spans a large body of water with varying depths and geological conditions,” says Mr Pai. Marine construction has its own unique set of challenges that include contending with corrosive saltwater, powerful tidal forces, and the possibility of seismic activity. The diversity of the seabed, with different types of soil types, rock formations and debris, requires specialised equipment and techniques to ensure structural integrity and longevity.
“This landmark project involved complex marine and foundation engineering, as it spans a large body of water with varying depths and geological conditions" - Vinayak Pai, CEO and MD, Tata Projects
Based on the nature of the ground strata, the foundations for the intertidal and marine sections were designed using piles or columns, while open foundations were constructed for the land and interchange sections. Pile foundations are constructed using reverse circulation drilling, a type of percussion drilling that uses compressed air to flush material cuttings out of the drill hole, ensuring safety, efficiency, and stability. The added advantage of using reverse circulation drilling machines was that it minimised construction noise. The extracted muck was collected in specific disposal barges that disposed of it at designated spaces, thereby ensuring zero water pollution and disturbance to marine life.
How the numbers stack up
- 21.8km: total length of the bridge, with ~16.5km over the sea
- 7.8km: length of Package 2 executed by Tata Projects and Daewoo E&C JV
- 3.6 lakh m3: the volume of concrete used — 2x the quantity used in the Statue of Unity, the world’s tallest statue
- 64,000 metric tonnes: the weight of the reinforcement steel used — 6X the steel used in the Eiffel Tower
- 5,900km: The length of post tension (high strength) strands used — more than 5x the distance between Delhi and Mumbai
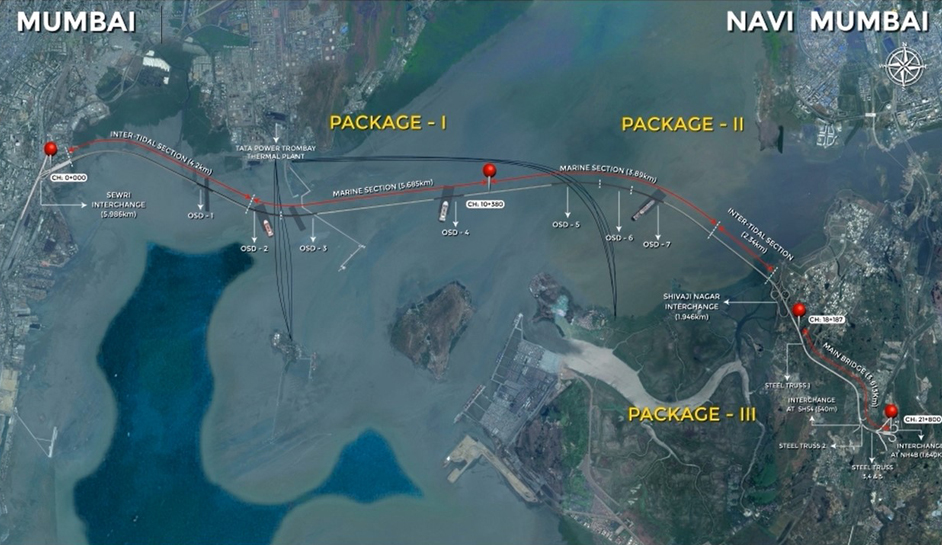
Technical prowess
The Mumbai harbour that the bridge crosses is a critical seaway used by boats and ships; it also supports the livelihoods of fisherfolk in the area. To facilitate safe movement of marine traffic, Tata Projects used orthotropic steel decks (OSD) — the first time this technology has been used in India. This unique grid-like engineered desk system is significantly lighter, with increased load capacity and strength when compared to concrete or composite girder bridges. The all-steel construction increases the structure’s life and requires less pile foundations, leading to reduction in construction time and lesser impact on the environment and ecosystem.
The steel used in the structure was sourced from four countries — Taiwan, South Korea, Vietnam, and Myanmar; then fabricated in Japan and assembled into the necessary spans at an assembly site in Karanja, Navi Mumbai. These spans were then loaded onto a 100m barge using self-propelled modular transporters for transportation to the construction site 15 nautical miles away, where they had to be lifted to a height of 27m.
“Managing logistics for materials and manpower across the long stretch of the sea link was difficult, especially given the marine environment,” says Mr Pai.
The 32-deck OSD section consumed 34,726metric ton (mt) of steel, with the highlight being the 180m deck — the longest in India — which alone weighed ~2200mt. All of this was done while maintaining a delicate balance between tidal variations, changing wind speeds, underwater currents, and seabed pipelines. “Atal Setu, India’s first 20km+ sea bridge, with its pioneering use of orthotropic steel decks represents a leap in engineering and sustainable design,” says Mr Pai. “The JV faced several challenges that required innovative solutions and meticulous planning to ensure its successful completion.”
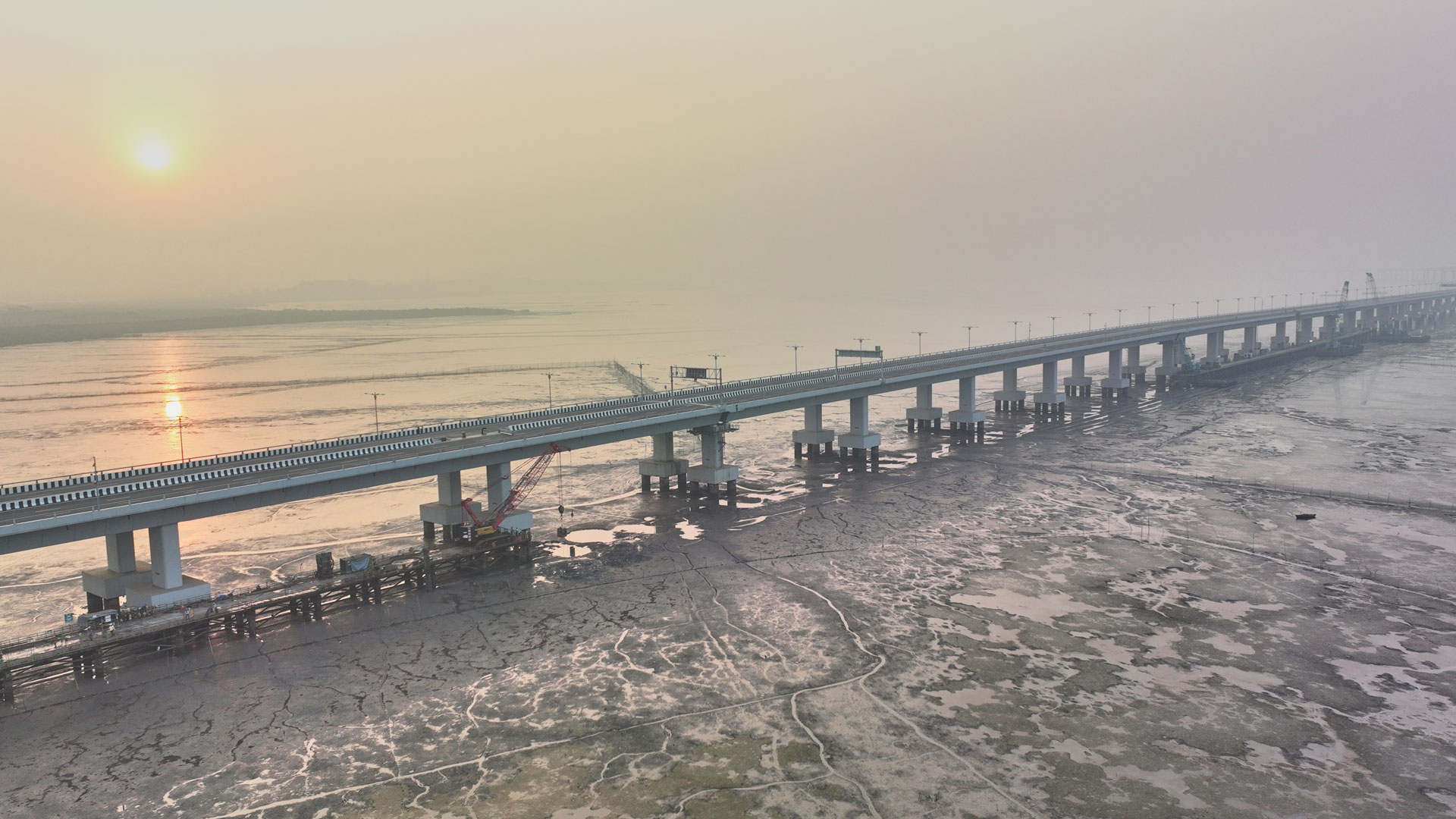
Navigating the deep
The pipelines in the seabed presented another challenge. They passed right through the alignment of the MTHL and were of a critical nature, as they transported fuel to and from offshore piers and onshore refineries. To ensure that these were undisturbed, project engineers had to stagger pier locations to maintain a minimum distance from these pipelines. The presence of these pipelines ruled out the option of building these superstructures using an access bridge — it would have been too risky or expensive, if not impossible, to build. Instead, the engineers designed and fabricated a unique 3,573m2 H-shaped barge that enabled them to erect the steel superstructures without needing to install any temporary structure on the seabed.
Links of concrete
The concrete portion of the bridge — over the intertidal and Package 3 land section — presented its own challenges. As is the case in modern bridge construction, the concrete segments were precast and transported for final erection at the site using launching gantries — specialised cranes that lift and place precast girders on piers. Given the timelines, precise planning was critical for timely delivery. Each gantry weighed 1,200mt and measured 135m. Shifting them in time was crucial and this was done using a rectangular barge with eight lifting towers, each weighing 615ton (t). These numbers underline the scale of the task at hand and the engineering prowess and project management capabilities of the teams involved.
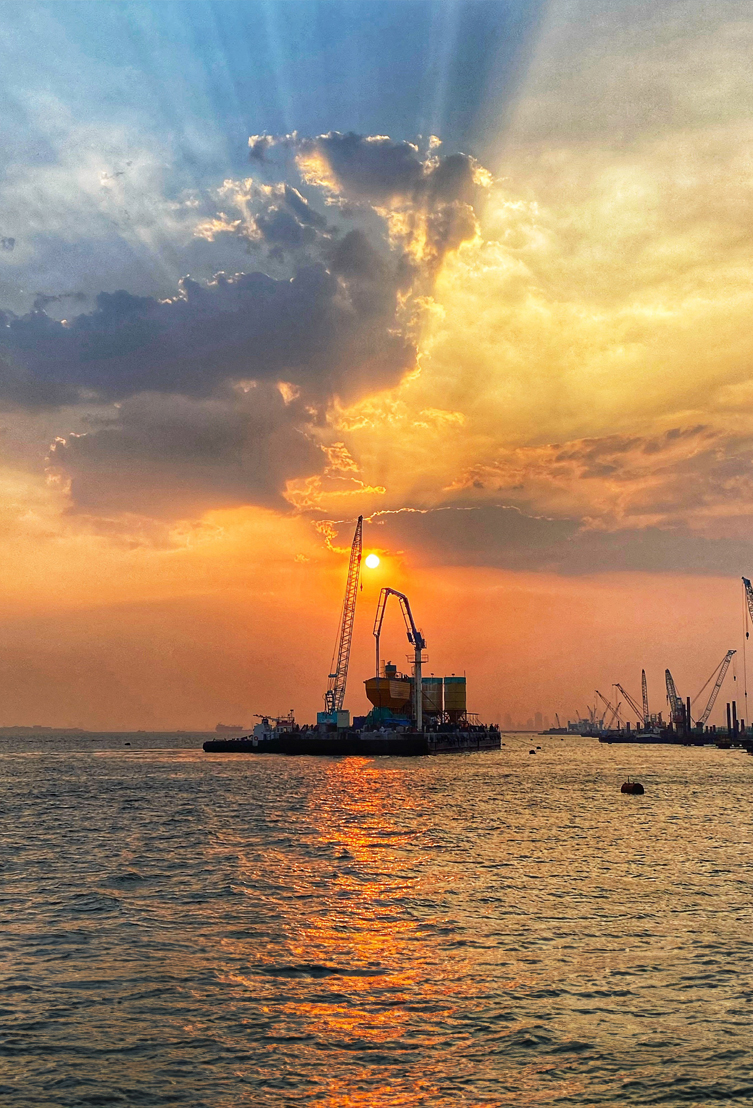
Teamwork at scale
The bridge is expected to serve as a vital transportation link for 120 years. Tata Projects employed robust quality control measures, sourced the best quality materials from global leaders — including reinforcement steel from Tata Steel — and the highest levels of engineering expertise to build a structure that could withstand the harsh realities of the maritime domain and the rigours of heavy traffic loads. Experts from around the world lent their expertise and knowledge to ensure that global standards were met.
“MTHL stands as a transformative force, elevating Navi Mumbai’s economic landscape and liberating Mumbaikars from traffic woes. It is not just a bridge; it is a promise of connectivity that will transform millions of lives.” - Vinayak Pai
A significant portion of the construction took place during the Covid-19 pandemic. Meticulous planning and attention to health practices and restrictions ensured little or no disruption, and lost time was made up in later stages with additional work fronts and personnel augmentation. The skill sets required in the project were varied, ranging from unskilled labour to specialised riggers for heavy lifting, seamen for marine operations, operators for heavy lifting cranes and other machinery, highly skilled operators for lifting jacks, and semi-skilled workers like carpenters, fitters, bar benders, welders — all working in mission mode. At its peak, there were 3,500 workmen working on Package 2, most of them belonging to communities adjoining the project site, ensuring generation of local employment.
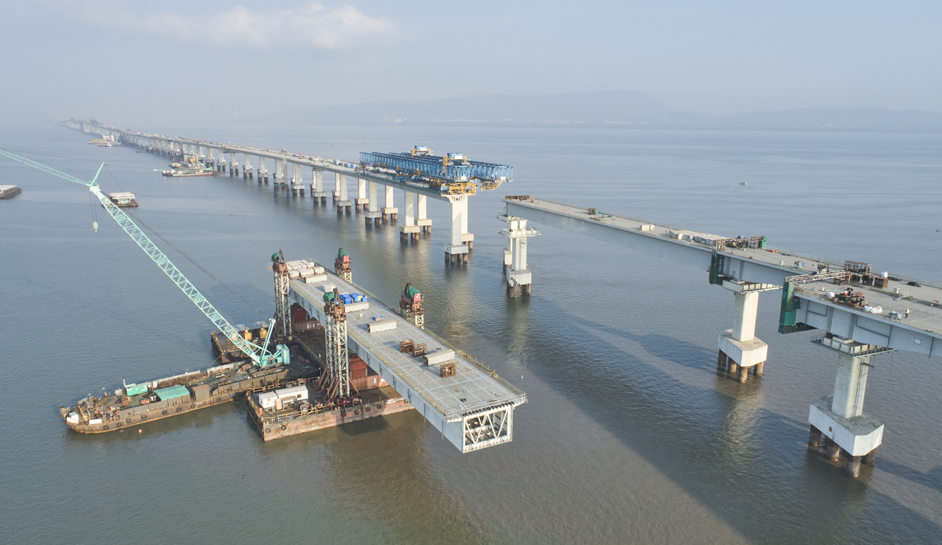
“Working at sea can be challenging,” says Mr Pai. “We navigated through challenges such as heavy and unpredictable monsoons, tidal variations, cyclones like Tauktae and Nisarga, working in sensitive flamingo habitats, and disruptions in supply chains due to Covid-19. Yet, we managed to complete it in the stipulated time frame of five and a half years.”
Proposed in 1981 by a steering committee headed by JRD Tata, former Chairman of Tata Sons, as a means to decongest the island city, “MTHL today stands as a transformative force, elevating Navi Mumbai’s economic landscape and liberating Mumbaikars from traffic woes, slashing travel time from 70 to 20 minutes,” says Mr Pai. “It is not just a bridge; it is a promise of connectivity that will transform millions of lives.”
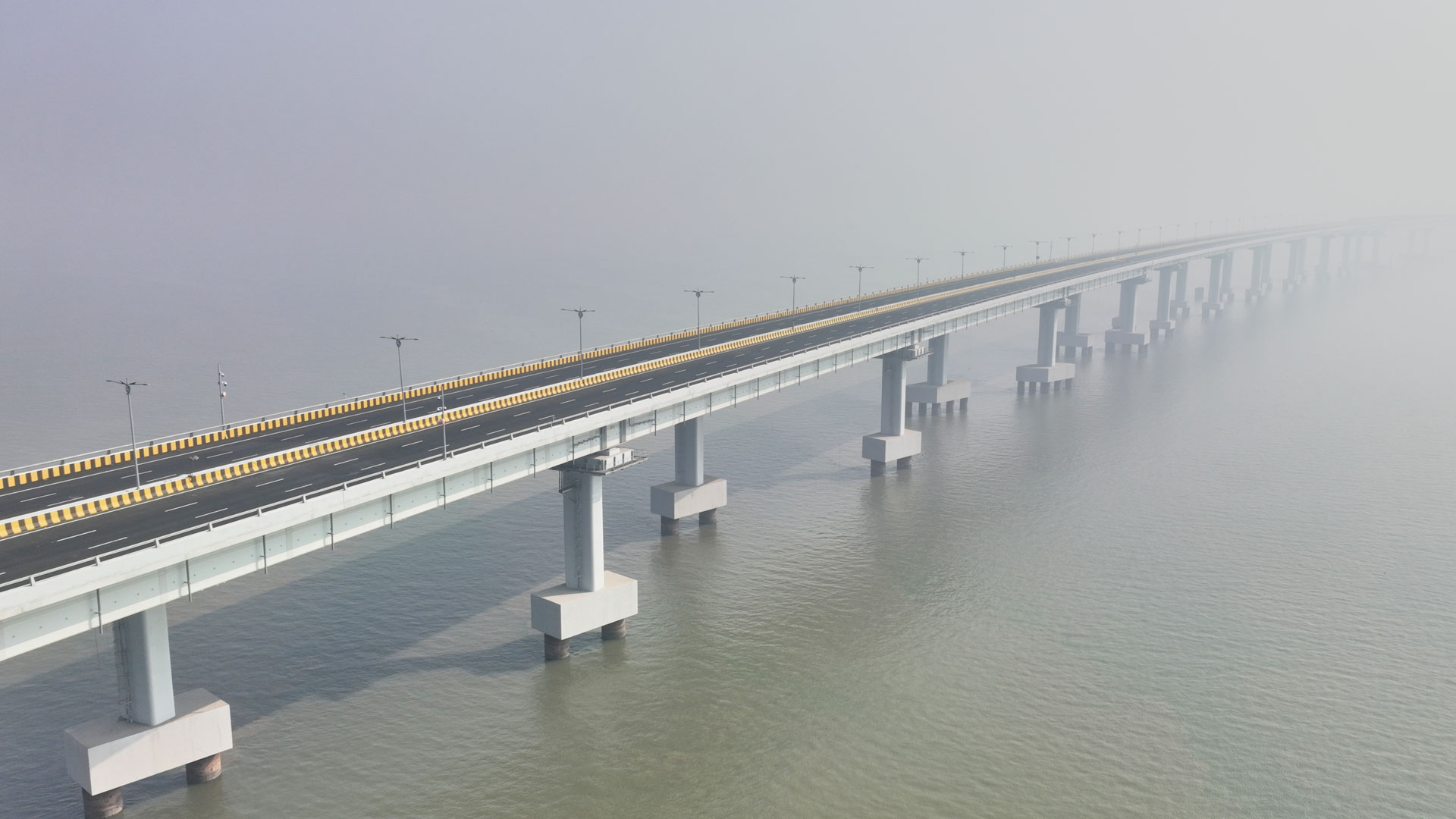
A coastal artery
The recommendation for the construction of a transportation link via the Sewri-Nhava Sheva route was first made in 1981 by a steering group that was chaired by the former Chairman of Tata Sons JRD Tata. The unique topography of Mumbai, a thin sliver of land jutting out to the Arabian Sea, places a premium on land available for commercial, housing, and utilitarian purposes. While improving accessibility, the MTHL is expected to accelerate expansion to the east, progressively decongest the city, and offer planners alternative spaces for growth. It will also ease the city’s connectivity to the upcoming Navi Mumbai airport, in addition to increasing economic growth opportunities in the adjoining Raigad district, enhancing infrastructure and availability of housing and commercial real estate.
- Haroon Bijli