November 2024 | 1344 words | 5-minute read
In the serpentine alleys of Ram Nagar in Varanasi, the air is filled with the rhythmic clacking of looms as deft hands weave beautiful silks, creating heirlooms that will be prized across generations.
Here, 28 weavers at the Angika Hathkargha Vikas Udyog Sahakari Samithi Weavershala are participating in a quiet revolution, showing the way towards a future where heritage and progress are no longer at odds. This Weavershala, which opened two years ago, was the first and largest of 20 set up by Taneira as part of its Weavershala initiative.
Started in 2022, Weavershala was born out of a need to create a sustainable livelihood for skilled weavers and artisans, by providing better living and working infrastructure, ensuring their timeless craft of handweaving continues to thrive in the modern world. For generations, weavers have hunched over pit looms in dark, congested, airless rooms, their fingers interlacing warp and weft with mathematical precision and a dexterity that is awe-inspiring. Their beautiful creations belie the harsh realities of their trade — repetitive, strenuous work in congested, substandard and unhygienic work environments that lead to several health and occupational problems. Plus, the daily wages they earn do not match the heavy labour and workmanship required — it takes a minimum of 15 days to craft a simple saree and up to nine months to craft an exclusive hand-woven traditional Banarasi saree.
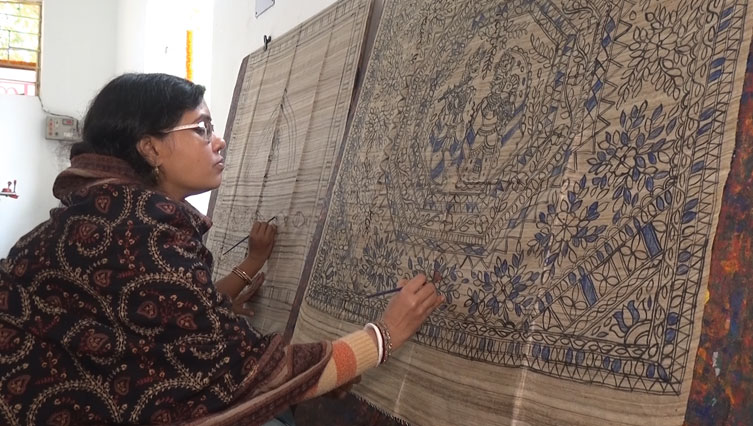
This situation has prompted the younger generation of craftspeople to turn to other trades, sometimes in bigger cities, in search of a steady pay cheque. But now, through Weavershala, Taneira is crafting a new narrative, one that is transforming the lives of the craftspeople behind the looms. The company set out to create a sustainable model for all stakeholders in the handloom value chain, especially focussing on uplifting the craftspeople, the most exploited link.
Starting with Varanasi, the company identified weaver-led organisations that it could collaborate with and set about modernising and, in some cases, building their community workspaces with better infrastructure and working conditions.
“When Taneira reached out to us, our sheds were in disrepair and we had no infrastructure. The company gave us the support we needed to start building the Weavershala." - Master weaver Sanjay Debnath
Over the last two years, 20 Weavershalas have been established across the country, in craft centres like Bhagalpur (Bihar), Champa (Chhattisgarh), Maheshwar (Madhya Pradesh), Gopalpur (Odisha), Mangalagiri (Andhra Pradesh), Coimbatore (Tamil Nadu) and Samudragarh (West Bengal), employing over 250 craftspeople, including dyers, spinners, loom-dressers and weavers. Some larger cities like Varanasi and Bhagalpur have more than one Weavershala. Often, entire villages or families are involved in the different stages of the production process. The sarees created by these Weavershalas are made of traditionally woven fabrics like Kadwa, Banarasi Silk, Tussar Silk, Khadi, Rangkat, Jacquard, Jamdani, Fulia, Chanderi, Maheshwari Silk and Mangalagiri Cotton, embellished with traditional crafts like Hazar Buti, Rangkat, Batik, Eknaliya, Dobby, Ikat and Madhubani painting. The sarees woven at these Weavershalas are sold at Taneira stores across the country.
Weaving in modernity
Back-breaking pit looms — the loom is set above a pit in the ground — have been replaced by ergonomically designed frame looms with comfortable seating. Electric jacquard machines, attached to the top of looms, and motorised lift mechanisms provide greater flexibility and speed, simplifying the process of creating complex patterns, designs and textures on various fabrics. Machine reels have replaced labour-intensive thigh reels that often cut into reelers’ skin and cause joint pains, while the introduction of loom production tracking devices helps maintain better control over quality and production. These modern additions have reduced the manual labour and physical strain required in hand weaving, increasing efficiency and production volumes, thereby leading to higher incomes for everyone.
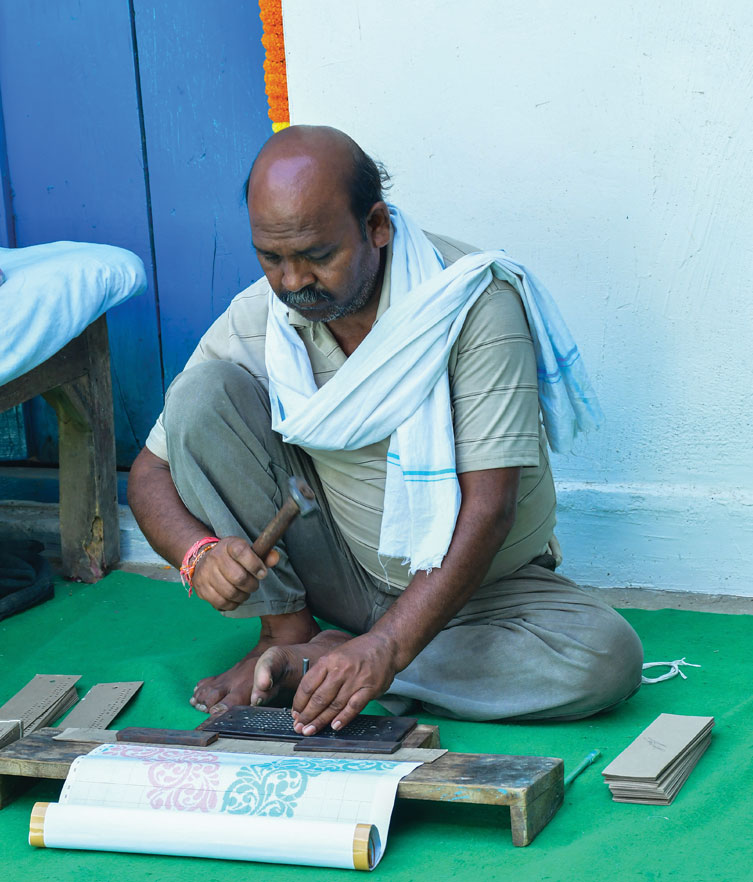
The transformation is not merely mechanical; it is also spatial and social. More often than not, weavers toil in solitude on age-old pit looms situated in dimly lit corners of their homes, sitting on the floor with their legs dangling into the pit to operate the pedals. Now, weavers who are part of the programme gather in their well-ventilated, brightly lit Weavershala, using modern tools to collectively weave exquisite drapes.
These modern Weavershalas also address a critical industry challenge — attracting young talent — and provide an opportunity for master weavers to pass on their knowledge to the next generation. Going ahead, the plan is to support and develop the existing Weavershalas, while also opening 10 new ones every year.
Spinning success
Samudragarh in West Bengal has a rich history of handloom craftsmanship, but the rise of mechanised textile production has led many artisans in the area to abandon their craft.
Master weaver Sanjay Debnath once ran a successful cooperative society of handloom weavers here. “But we lost all our weavers and got into debt because of the power looms,” he says. “When Taneira reached out to us, our sheds were in disrepair and we had no infrastructure. The company gave us the support we needed to start building the Weavershala. We started approaching women who were weaving at home and encouraged them to join the Weavershala as it would offer regular work as well as better wages and working conditions.
The initiative’s masterstroke, however, lies in its understanding that dignity and pride are the truest currency of labour
The old shed was renovated with better facilities, and we now have 10 women weavers working here — making us the first all-women Weavershala in the country. Starching specialists, who knew how to strengthen the cotton yarn, had also disappeared. With the establishment of the Weavershala, these specialists have also returned. The Weavershala system is a lot more efficient; our weavers can produce at scale, leading to higher incomes.”
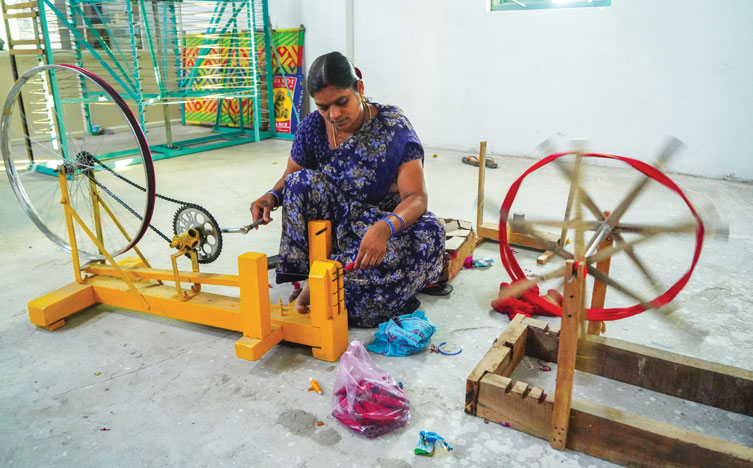
Crafting dignity
The initiative’s masterstroke, however, lies in its understanding that dignity and pride are the truest currency of labour. Craftspeople in the Weavershalas now sport crisp uniforms and carry ID cards, tangible tokens of professional pride and the respect accorded to them as masters in their trade. Fair wages ensure that their compensation is commensurate with the artistry they produce.
The initiative’s reach extends beyond the loom. It has created a robust supply chain, doing away with exploitative middlemen, and taking a comprehensive approach to improving artisans’ lives, not just their work, so that they can cater to evolving market demands without sacrificing their artistic heritage. In the delicate tapestry of tradition and innovation, Taneira’s Weavershalas are a testament to the power of mindful progress.
- Kermin Bhot